When expanding your roofing sheet business or selecting a new roofing sheet making machine, it’s important to consider various details to optimize your operations. Here are some key points to analyze:
1. Enhance Machine Automation:
If your current roll forming machine operates with a semi-automatic design, requiring manual collection of roof sheets and manual uncoiling, it’s advisable to upgrade to a hydraulic decoiler and an automatic stacker. This upgrade significantly improves your machine’s efficiency and reduces labor costs.
We highly recommend a hydraulic decoiler equipped with rails beneath the base frame, as shown in the photo below. This allows the decoiler to easily move and work with different roll forming machines.
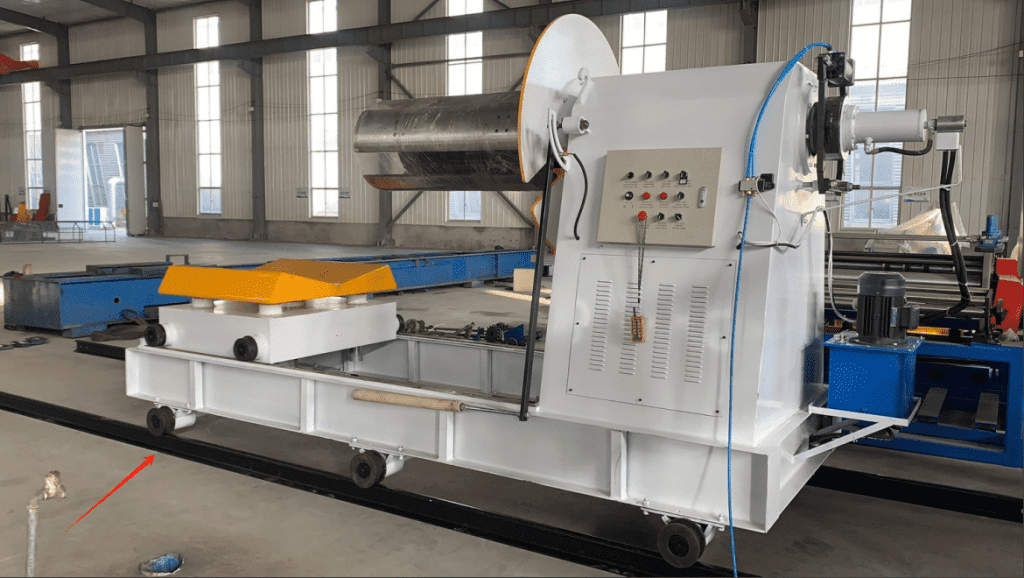
2. Select Gear Box Transmission and Cast Iron Machine Structure:
Opting for a gear box transmission ensures faster machine operation, providing rapid and stable performance during start-up and shutdown. We have designed and manufactured numerous machines with this feature for various clients.
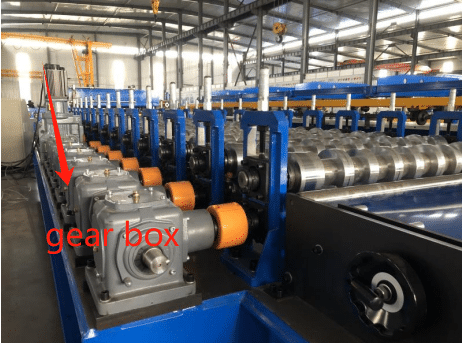
3. Implement Tracking Cutting Design:
Choose a machine with a tracking cutting feature that continuously cuts without stopping as the roof sheet runs through the machine. This design can reach a maximum speed of 50 m/min. Additionally, a servo motor ensures fast and stable cutting performance.
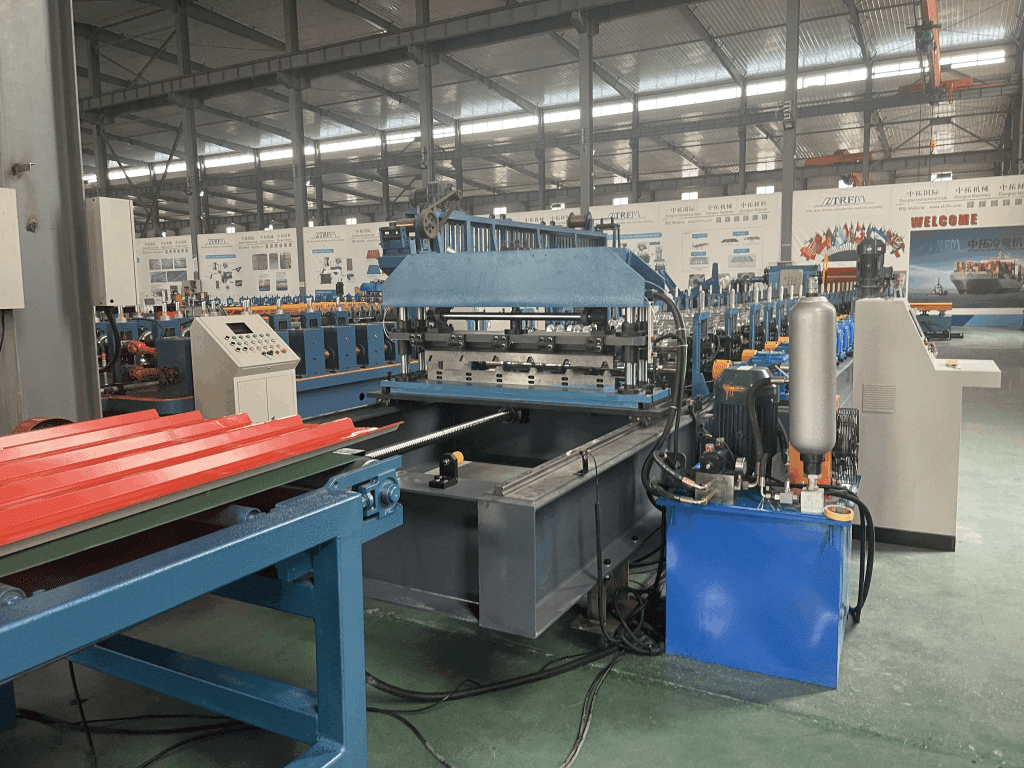
By focusing on these aspects, you can significantly improve your roof sheet business operations and machine performance.