In this overview, I will walk you through our state-of-the-art punching line, which is teeming with sophisticated automation and cutting-edge technology. I’ll be providing a thorough examination of each element within this system. Central to this setup is a robust 10-ton hydraulic decoiler, complete with an upper bender for effortless coil feeding.
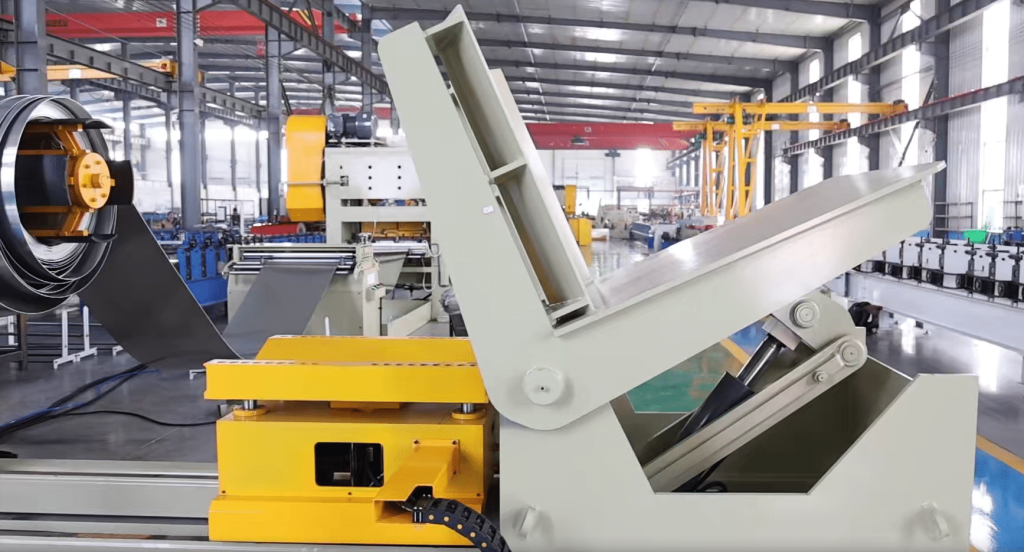
Let’s examine the advantages of this hydraulic decoiler more closely. To begin with, it includes an oiling mechanism for the press arm, which guarantees smoother operations and a longer service life. Furthermore, all electrical wiring is meticulously arranged in cable trays, a design choice that not only improves safety but also enhances the machine’s longevity. The cover table and its surrounding zone are crafted to safeguard these lines, preserving the machine’s sleek appearance and promoting a safe working environment.
The V-shaped construction of our loading cart is specifically engineered to prevent any damage to the coils during loading, such as surface scratches. The upper bender, once loaded with coils, deftly bends and feeds them into the system, a process I will demonstrate later.
Safety is a paramount consideration in the design of this decoiler. It is equipped with limit switches and wiring encased in plastic for secure operation. Operators have the flexibility to control the machine either locally or remotely, with a control range of 10 to 15 meters, thus eliminating the need for close proximity to the equipment. Moreover, a sensor detects the presence of coils below the machine and automatically stops the decoiler to maintain the ideal speed and ensure seamless coordination with the rest of the production line.