T Bar Ceiling Roll Forming Machine

1. Speed: can reach 0-45 m per minute
2. Machine automaticality: after feeding the material into machine, the machine will running automatically, you just need one worker packing t bar. Save much labor.
3. Machine control: By PLC system, length, quantity and speed can be adjust on touch screen.
4. Machine operate: Easy to operate, normally speaking one week then you can learn how to run it.
5. The main T grid made by our machine is beautiful in shape and solid when using.
Profile drawing for reference:
The whole T grid ceiling system combined with main tee, long cross tee, short cross tee and wall angle. Here is attached the standard dimension for each part for your reference.
Main tee: 38x24x3600 mm
Long cross tee: 28x24x1200 mm
Short cross tee: 28x24x600 mm
Wall angle: 22x22x3000 mm
Main T bar roll form machine processing flow:
Uncoiling—Feeding material—Roll forming—Hydraulic cutting—Pinching the T bar from roll forming machine to punching machine—Punching holes—Product collect table
Main T Roll Forming Machine Main Technical Parameters
Raw material: PPGI & GI
Forming speed: 0-45 m per minute
Forming stations: 18 stations
Shaft material: 45# steel with quenched treatment precision machined
Roller shaft diameter: 40 mm
Voltage: 380 v 50 hz 3 phase or customized as your request
Roller material: Cr12 with quenched treatment
Transmission type: By chains
Material of blades: Gcr12mov quenched
1.Two sets Manual Decoilers
Need two sets decoilers, one loading basic material, another set loading face material.
a. Inner diameter: 450-550 mm
b. Coil max width: 300 mm
c. Max carrying capacity: 1500 kg
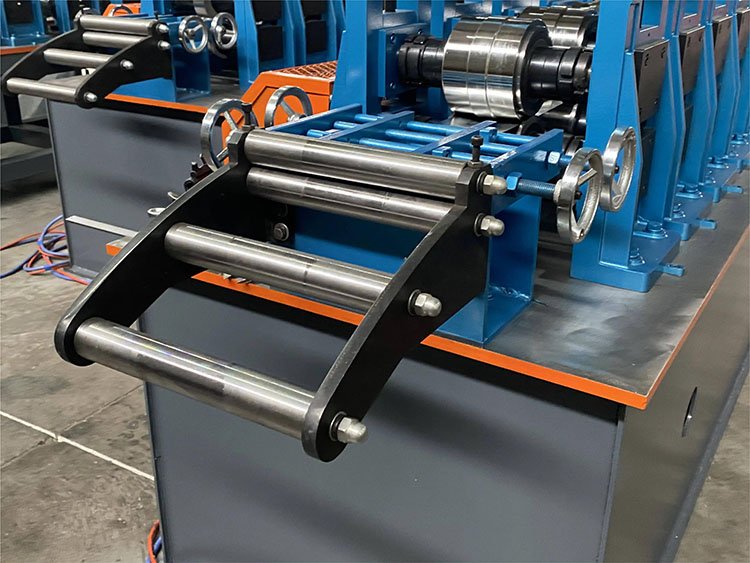
a. Number of forming steps: 18 stations
b. Shaft material: 45# steel with quenched treatment precision machined
outer diameter: 40 mm
c. Roller material: Cr12 with quenched treatment
d. Transmission type: By chains
e. Drive motor power: 4kw
f. Voltage: 380 v 50 hz 3 phase
g. Forming speed: 0-25 m per minute
h. Structure: Independent stand (cast steel)
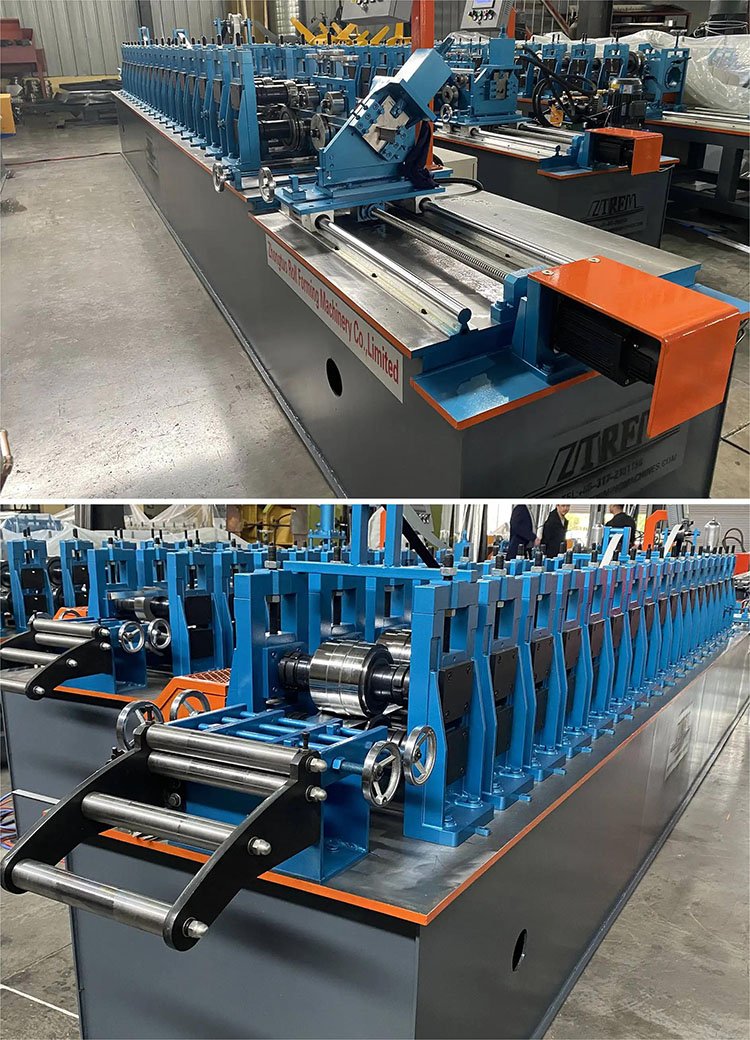
It adopts the hydraulic drive and automatic location to decide the dimension and cut the target products.
Cutting type: servo tracking cutting Servo motor power: 1.2 kw
Power supply: 3 kw hydraulic power Material of blades: Gcr12 mov quenched
Components: It contains one set of cutting tools with one hydraulic tank and one cutter machine.
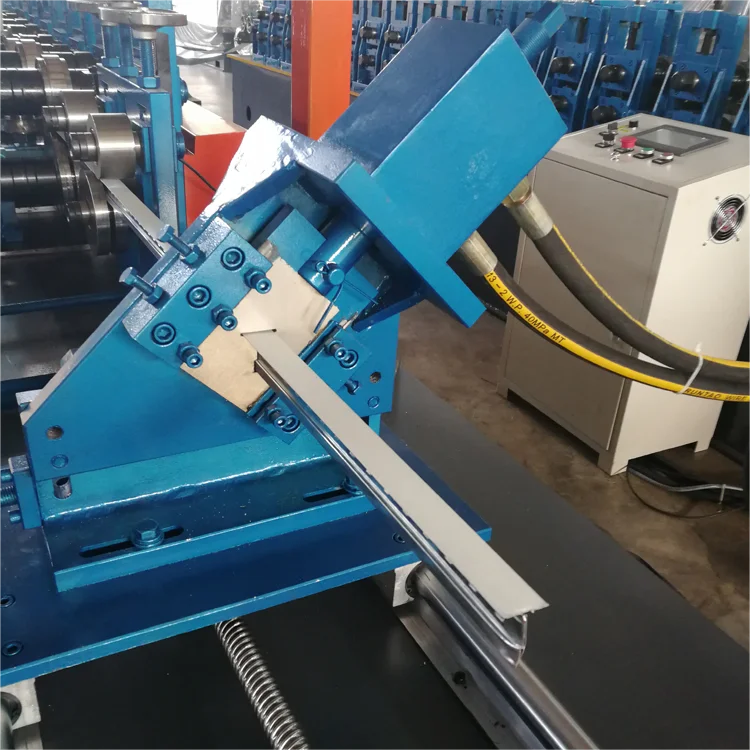
5.PLC control system
Adopted PLC, transducer, touch panel to ensure high speed with stability, precision and lifetime.
Language: Chinese and English
Automatic length and quantity measurement
Length Tolerance: 3 m+-1.5 mm
Computer operating panel: touching screen and button together
Equipped with movable switch, air break, radiator, transformer and electric leakage protector for operation convenience and safety.
6.Punching System
Processing molds: 3 sets
Mould material: Skd 11 (Cr 12)
Servo motor power: 1.2 kw
Power supply: 7.5 kw hydraulic power
Have logo pressing function
7. Hydraulic Station
Processing molds: 3 sets
Mould material: Skd 11 (Cr 12)
Servo motor power: 1.2 kw
Power supply: 7.5 kw hydraulic power
Have logo pressing function
8. Electric Control System For Punching
Processing molds: 3 sets
Mould material: Skd 11 (Cr 12)
Servo motor power: 1.2 kw
Power supply: 7.5 kw hydraulic power
Have logo pressing function